Nitrogen Generator: A Key Force in Ensuring Quality in the Pharmaceutical Industry
Nitrogen generators have a wide range of applications in pharmaceutical production, packaging, and transportation.
In the pharmaceutical industry, every link in the chain, from drug production to packaging and transportation, has stringent environmental and condition requirements. Any slight mistake may affect the quality and safety of the drug. As a device capable of producing high-purity nitrogen, nitrogen generators play a vital role in the pharmaceutical industry and have become key equipment for ensuring drug quality.
I. Applications of Nitrogen Generators in Drug Production
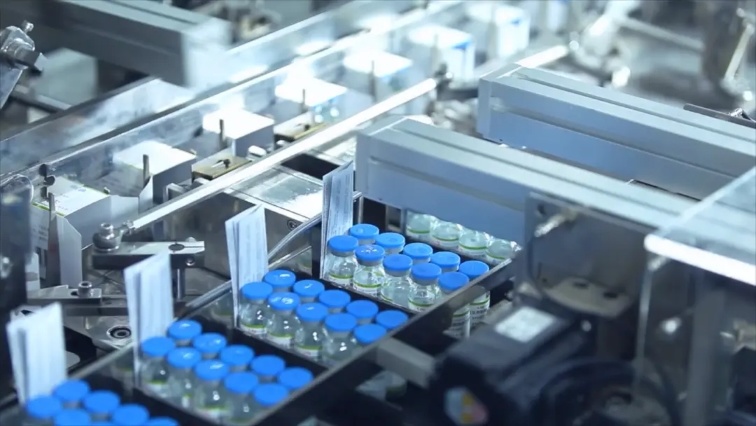
(1) Synthesis of Raw Materials
In the synthesis of raw materials, many chemical reactions have extremely high environmental requirements, especially regarding oxygen sensitivity. The presence of oxygen may trigger unnecessary oxidation reactions, leading to raw material loss, reduced product purity, or even changes in the drug's chemical structure, affecting its efficacy. Nitrogen generators can provide high-purity nitrogen to create a near-oxygen-free inert environment, effectively preventing oxidation reactions. For example, in the synthesis of certain antibiotics, continuously introducing nitrogen into the reaction vessel to eliminate oxygen interference allows the reaction to proceed as planned, ensuring the integrity of the drug molecule structure and thus guaranteeing the quality and efficacy of the raw materials.
(2) Bio-fermentation
Bio-fermentation is an important process for producing many drugs, such as vaccines and enzyme drugs. During fermentation, the growth and metabolism of microorganisms require specific environmental conditions, and a sterile, low-oxygen environment is crucial. The pure nitrogen produced by the nitrogen generator can, on the one hand, serve as a sterile gas source, reducing the risk of contamination during fermentation; on the other hand, by adjusting the nitrogen concentration in the fermenter, the dissolved oxygen content can be controlled, providing the most suitable growth environment for microorganisms. In addition, introducing nitrogen can also stir and mix the fermentation broth, promoting the uniform distribution of nutrients, improving fermentation efficiency and product quality. At the same time, the carbon dioxide produced during fermentation can also be promptly removed using nitrogen purging to maintain the stability of the fermentation environment.
(3) Drug Drying
Drug drying is an important step in ensuring drug quality and stability. Traditional drying methods may cause drug moisture absorption and oxidation due to moisture and oxygen in the air. The dry nitrogen provided by the nitrogen generator can displace moist air during drug drying, reducing environmental humidity and preventing oxygen from contacting the drug, preventing oxidation and deterioration. For example, for some moisture-sensitive drug preparations, such as certain granules and powders, using nitrogen protection during drying can effectively control moisture content and maintain the stability of the drug's physical and chemical properties.
II. Applications of Nitrogen Generators in Drug Packaging
(1) Preventing Oxidation and Extending Shelf Life
Most drugs are susceptible to oxidation during storage due to oxygen, leading to discoloration, deterioration, and reduced efficacy. The high-purity nitrogen produced by nitrogen generators is widely used in drug packaging. By filling the packaging container with nitrogen to displace the air, the oxygen content is significantly reduced, effectively inhibiting the oxidation process and extending the shelf life of the drug. For example, filling ampoules and infusion bags of injections and infusions with nitrogen can prevent oxidation and deterioration of the drug solution; for blister packaging of tablets and capsules, a nitrogen environment reduces the risk of moisture absorption and oxidation, ensuring the stability of drug quality within the expiration date.
(2) Moisture Prevention and Maintaining Drug Stability
In addition to oxygen, moisture is another important factor affecting drug quality. Many drugs are hygroscopic and easily absorb moisture from the air, causing deliquescence, hydrolysis, and other reactions, leading to changes in drug properties and degradation of active ingredients. Using dry nitrogen in drug packaging can reduce the humidity inside the packaging, creating a low-humidity environment to prevent hygroscopic drugs from absorbing moisture. For example, some traditional Chinese medicine preparations and biochemical drugs are sensitive to humidity, and nitrogen packaging can effectively maintain drug stability, ensuring that the quality is not affected during storage and transportation.
(3) Inhibiting Microbial Growth
Microbial contamination is one of the key issues in drug quality control, which can lead to drug deterioration, failure, and even serious harm to patient health. A nitrogen environment is not conducive to the growth and reproduction of most aerobic microorganisms. Filling the drug packaging with nitrogen can reduce the possibility of microbial growth in the packaging, helping to maintain the sterile state of the drug and improve drug safety. In particular, for some sterile preparations, such as powder injections and lyophilized powder injections, nitrogen protection above the bottle stopper can effectively reduce the oxygen and microbial content in the bottle, preventing drug contamination.
III. Applications of Nitrogen Generators in Drug Transportation
During transportation, drugs face challenges from various environmental factors such as temperature, humidity, and vibration, and are also susceptible to oxygen and microorganisms. To ensure the stability of drug quality during transportation, nitrogen generators also play an important role. By using modified atmosphere packaging technology and filling the drug transport packaging with an appropriate amount of nitrogen, a relatively stable inert environment can be created, reducing the contact between the drug and the external environment and lowering the risk of oxygen and moisture erosion. For example, for drugs that require long-distance transportation or storage in special environments, such as biological products and vaccines, nitrogen packaging can provide additional protection for the drugs, ensuring that their quality is not affected during transportation, guaranteeing the effectiveness and safety of the drugs.
IV. Special Requirements for Nitrogen Generators in the Pharmaceutical Industry
(1) High-Purity Nitrogen
The pharmaceutical industry has extremely high purity requirements for nitrogen, usually requiring more than 99.9%, and even in some special applications, the purity needs to reach more than 99.999%. High-purity nitrogen can reduce the impact of impurities on drugs, ensuring the purity and stability of drug quality. For example, in the production and packaging of sterile drugs, only by using ultra-high-purity nitrogen can the strict quality standards be met to prevent drug contamination due to impurities in the nitrogen.
(2) Stable Flow Rate and Pressure Control
In the production, packaging, and transportation of drugs, different process stages have different nitrogen flow rate and pressure requirements, and stability is required. The nitrogen generator should have flow control and pressure regulation functions to provide a stable nitrogen supply according to actual production needs. For example, in the synthesis reaction of raw materials, the nitrogen inflow rate and pressure need to be precisely controlled according to the reaction process to maintain the stability of the reaction; in drug packaging, stable nitrogen flow rate and pressure can ensure uniform gas displacement in the packaging, guaranteeing packaging quality.
(3) Hygienic Materials and Low-Pollution Design
Since the nitrogen produced by the nitrogen generator is in direct contact with pharmaceuticals or the pharmaceutical production environment, its materials and design must meet the hygiene standards of the pharmaceutical industry. The contact parts of the nitrogen generator are usually made of stainless steel or other hygienic-grade materials to prevent impurities from contaminating the nitrogen. At the same time, the equipment's structural design should minimize dead corners and dust accumulation points to facilitate cleaning and disinfection, reduce the risk of microbial growth, and ensure that the entire nitrogen production and supply process meets the requirements of Good Manufacturing Practice (GMP).
(4) Reliability and Stability
Pharmaceutical production is a continuous process, and any equipment malfunction can lead to production interruptions, causing significant economic losses and even affecting drug supply and patient treatment. Therefore, the nitrogen generator must have a high degree of reliability and stability, capable of continuous operation for extended periods without failure. The equipment should use high-quality components and advanced manufacturing processes, and be equipped with a complete automated control system and fault diagnosis function to monitor the equipment's operating status in real time, promptly identify and resolve potential problems, and ensure the continuity and stability of nitrogen supply.
5. Conclusion
Nitrogen generators play an irreplaceable role in various stages of pharmaceutical production, packaging, and transportation in the pharmaceutical industry, and are key equipment for ensuring drug quality and safety. With the pharmaceutical industry's increasing demands for drug quality, nitrogen generator technology is also constantly developing and innovating to meet the increasingly stringent needs of the pharmaceutical industry. In the future, nitrogen generators will continue to play an important role in the pharmaceutical field, providing strong support for promoting the high-quality development of the pharmaceutical industry.
Other areas
Oil storage and pressurized pipeline cleaning and purging of oil and gas wells, nitrogen sealing, nitrogen displacement, solvent recovery.
Used for food preservation and grain storage, pest control, food drying and sterilization, quick freezing of food, etc.
Provide the necessary gas raw materials for the preparation of new energy materials, battery production, and create an inert gas environment.
Ensure the manufacturing of electronic components and the stable operation of equipment, providing gas support for maintenance, combustion assistance, cooling, and other aspects related to thermal power generation equipment.
Nitrogen generator: Prevents oxidation, inhibits bacterial growth, and produces odors in biopharmaceuticals, providing protection throughout the process. Oxygen generator: Provides an oxygen-rich environment.
When signs of fire occur in the goaf or other locations, nitrogen injection is needed for fire prevention. The nitrogen device is lowered into the mine. It is used for annealing protective gas and sintering.
Used in the aerospace composite field, providing the necessary inert atmosphere for the molding and reinforcement processes of large carbon fiber composite wings.
Provide protection for the safety of oil and gas reserves, prevent oxidation, nitrogen sealing, and ensure dust suppression, fire prevention, and nitrogen sealing for coal reserves.